1. U.S. Economy Trends – A Quick History Lesson
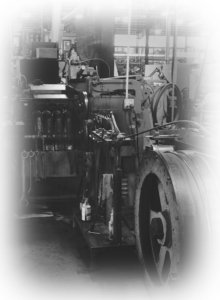
Since the 1960s foreign suppliers have continued to capitalize on their growing ability of low cost production. Cheap labor and lenient standards, among other things, have allowed oversea producers to maintain a drastically lower price range (5% – 20% depending on the product) as compared to domestic manufacturing in the United States. China eventually surpassed the U.S. in 2010, becoming the #1 leading manufacturer in the world.
Changes in healthcare, standard of living, labor laws, taxes, etc… significantly impact the overall cost of production in America. Due to increased operational costs throughout the U.S., a large number of companies have strategically moved their business to a cheaper alternative. In return, many U.S. market segments continue to suffer the growing import craze induced by foreign competitors. While constantly battling trade deficit issues, America still holds the 2nd place title in global manufacturing.
DID YOU KNOW?
Manufacturing workers in America are among the most productive worldwide in terms of hourly output. Producing over 18% of the world’s goods, the U.S. has remained a leading supplier for decades. Despite nationwide plant closures, increased unemployment rates, and recessions; U.S. manufacturing as a whole is in for the long-haul.
According to recent on-shoring and market economy trends, the light at the end of the tunnel could be much brighter than expected.
Production tides are forecasted to return once more to American soil, and here’s why.
INDUSTRY ARTICLE: Trending Update
If you haven’t read Thomasnet’s article; 83% of North American Manufacturers Are Likely to Reshore Their Supply Chains in 2021, you need to do so now! Current and forecasted reshoring trends are not merely opinions, but rather valid claims backed by powerful market research. This is a must read!
2. Domestic Manufacturing – Is Growing
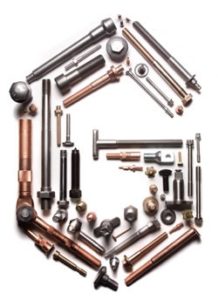
The global economy may be one of the biggest factors in manufacturing growth, but there is one thing that matters more – DOMESTIC DEMAND. As defined in the Cambridge Business Dictionary, domestic demand is “the total amount of money that is spent on goods and services by the people, companies, and government within a particular country, or that would be spent if the goods and services were available.”
According to recent feedback produced by Thomas 2019 Survey on U.S. Manufacturing, the majority prefer to buy products “Made in America”. The survey also reported that the perception of domestic manufacturing is improving, and considered highly important to the U.S. economy.
• 95% stated manufacturing is important to the U.S. Economy
• 87% stated a strong manufacturing sector is important to national security
• 75% stated sustainability has a large impact on goods they purchase
• 60% stated they would encourage someone to pursue a manufacturing career
Regardless of closing foreign wage gaps, ongoing trade wars, and new competitive pressures; most of America’s manufacturing growth can be largely attributed to the following:
– The utilization of expeditiously advancing technology –
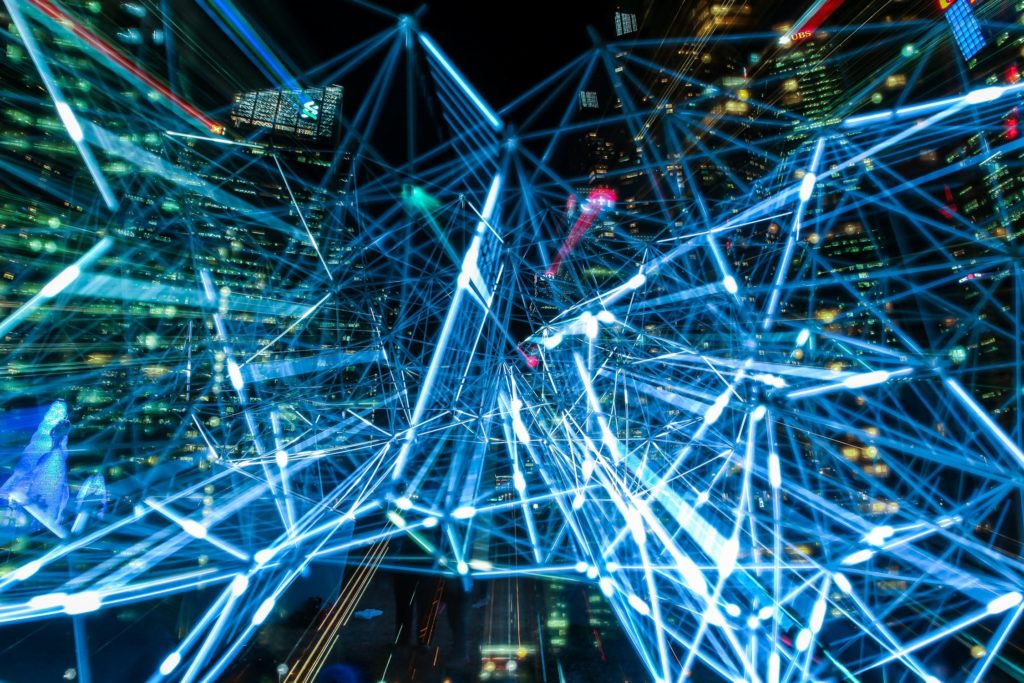
Applied science is quickly changing nearly every production asset in U.S. factories today. Those who have invested in this new age strategy are reaping the benefits of cost reduction through improved manufacturing processes. Here are a few aspects that characterize today’s modernization of American manufacturing.
• Automation & Robotics – Increased output per hour
• Advanced Planning and Scheduling – Logarithmic approach and AI analysis
• Smart Power – Increased energy efficiency and electric power generation
• Smart Manufacturing – Fully connected systems to maximize efficiency
• Process Improvements – Reconstructive improvements to current processes
• Lean Manufacturing – Eliminating waste from manufacturing processes
• Continuous Improvement – A method for identifying cost saving opportunities
3. American Production – Supports America
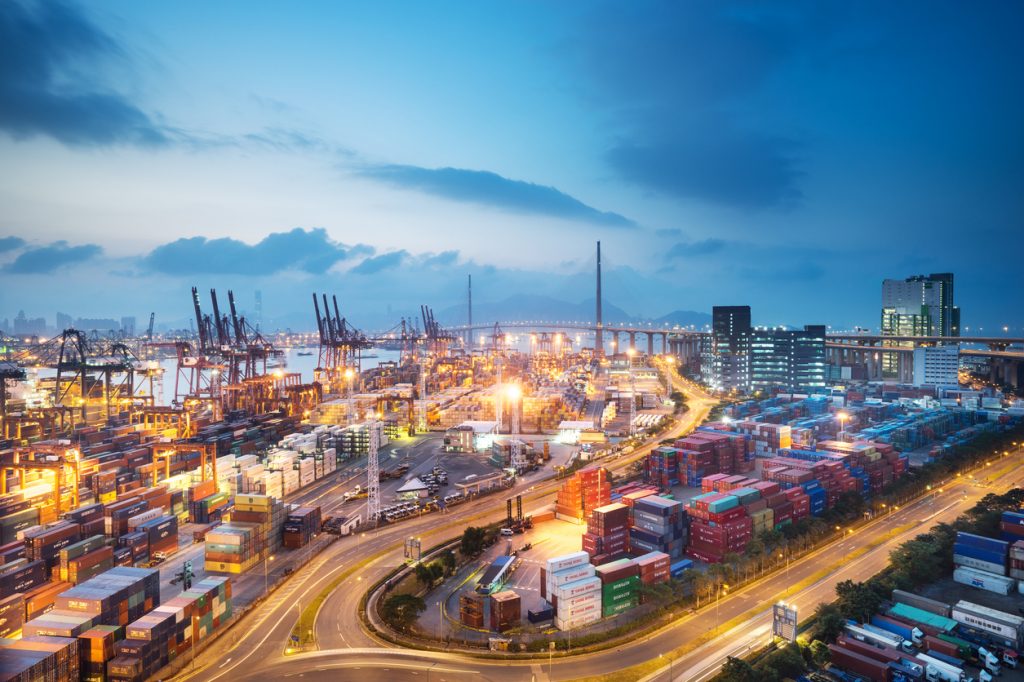
Manufacturing as a whole is the largest sector in the U.S. economy, which also happens to be the largest and most productive economy in the world. We hold a vast majority of the top brands, lead the globe in technology, and are home to the world’s best colleges. Our economy is also structured to be highly competitive, and to top it off – the U.S. dollar is king!
With that being said, buying domestically makes our nation more profitable and strengthens the U.S. economy as a whole. Next time you’re facing a “Made in America” decision, consider the following.
• Buying domestically increases domestic demand
• Domestic demand creates jobs
• Job creation reduces Government expenditures for assistance programs
• It strengthens and grows the domestic supplier base
• Your supply chain visibility will be improved
• Increased economic stability
• Significant risk reduction associated with trade tariffs and wars
Of all the benefits to buying products Made in America, increasing domestic demand is likely to be the most important of all. Did you know that domestic demand is the most influential driver to promote competitive advantage of American goods?
Competitive advantage is the ability to supply equal or superior goods in ways that generate a greater overall value. There are multiple factors compiling these advantages among suppliers, which exhibit both differential and comparative advantage components.
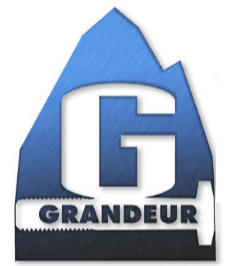
Strong Branding
High Quality
Improved cost structuring
Value added services
Creating superior products
Advanced technology
In addition, America is continually becoming more competitive from an operational standpoint primarily due to efforts in maximizing energy efficiency, increased supplier performance, and the narrowing gap of labor costs between U.S. and foreign entities.
4. American Made – Means Value Added
In case you were wondering, the answer is YES! Domestic suppliers will add value to your company, and it’s much more than what foreign competitors can offer. Aside from the economics, continuous improvements, and other various reasons why you should buy American… here are the value added perks you won’t get overseas.
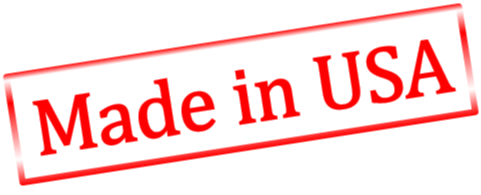
– High quality standards – both environmental and finished product
– Eliminate counterfeiting – will not substitute “fakes” to gain a larger margin
– Risk reduction – rework, loss, recall, repairs, and late orders
– Smaller carbon footprint – green manufacturing practices and decreased logistical distance
– Outstanding customer service – home grown American people and clear communication
– Highly value “Made in America” – which means they will take pride in making your product
– Reduced travel expenses – shorter travel distance for business trips and plant visits
– Valued relations – American suppliers grow lasting relationships with their customers

5. Domestic Delivery – Time Is Money
Shorter lead times and the ability to react quickly are also huge benefits of utilizing a domestic supply base. A vast majority of domestic suppliers offer various programs, such as: VMI, stock & release, JIT, and min-max agreements – which reduce customer carrying costs and better serves their individual ebb and flow of demand.
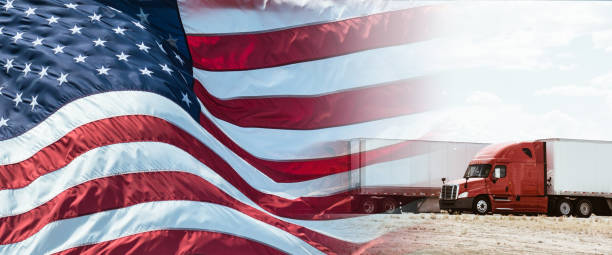
To top it all off, local suppliers will make on-the-fly adjustments and are superior at filling rush orders and drop-ins; which will positively impact standardized inventory levels and cost as well. American manufacturers are also highly flexible, and will accommodate to unique customer needs when others can’t. It’s hard to beat suppliers willing to go this extra mile and is an excellent way to win new business!
Domestic manufacturing will ultimately save you time, and in this world – TIME IS MONEY!
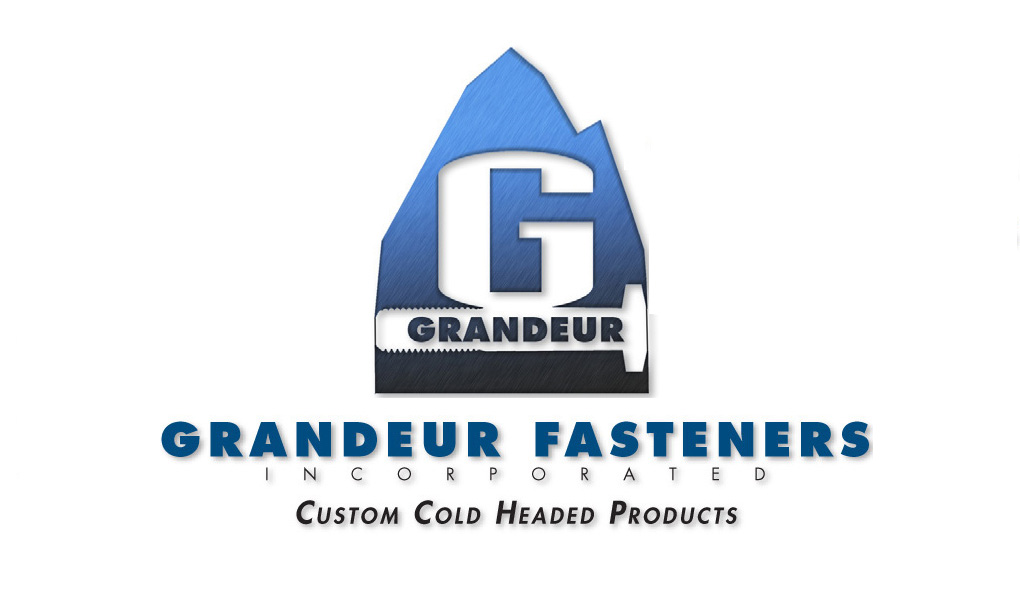
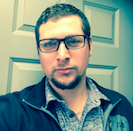
By: Derrick Pledger
Inside Sales and Marketing
Phone: 479-489-5168
Grandeur Fasteners, Inc.
sales@grandeurfasteners.com