Costing is one of the most influential factors in our manufacturing world today. There is an ongoing trend among companies across the globe to become “cost driven.” By reducing expenditures in a manufacturing process, profit is therefore increased by spending less to produce a product. Custom Cold headed fasteners and components have come a long way in the past 100 years, and now is the time to consider your options.
But what happens when you’ve exhausted all other options, and those monthly numbers still aren’t reaching expectations?
If you’re looking for an economical solution to an expensive fastener or component problem, custom cold headed parts could be the answer to increasing your bottom line.
Custom Cold Headed Fasteners = Savings
Buyers are often looking for the cheapest and fastest suppliers for parts needed to run production. Understanding “why” cold heading can result in savings is crucial to knowing whether it is an option for you.
Here are 10 reasons why material planners, purchasing agents, and engineers look to cold heading for solutions:
- Capable of converting two to three parts into one
- Reduction in part weight with no effect on function
- Virtually no yield loss on all parts
- Enhanced material flow creates stronger components
- Large volumes generate better pricing
- Able to achieve tolerances up to .002 and excellent quality
- Unlimited applications
- Can form metals not suitable for machining
- Cold heading is cheaper and faster than machining
- Shorter lead times from faster production rates
Purchasing machined components can be expensive and time consuming, resulting in massive amounts of waste and extended lead times. Not only is cold heading cheaper than machining, but it is more efficient than any other fastener and component manufacturing process. It requires less material, less energy, less time, and less manpower – equating to reducing cost.
So how much can you really save? You’d be surprised how much a few cents on the dollar can make a difference.
Here’s an example:
1,000,000 custom fastener or component X .50 ea (machined) = $500,000
1,000,000 custom fastener or component X .35 ea (cold headed) = $350,000
That’s a savings of $150,000! The reduction in material waste alone is enough to reduce the cost substantially for the manufacturer, thus providing a better part for a better price. A single cold heading machine can produce up to 30,000 parts in a single shift. Theoretically, 1,000,000 hex bolts could be manufactured in about 30 days.
The Fine Print
At this point, you may be wondering about the limitations of cold heading and what exactly can be achieved through the cold forming process.
Given today’s technology and experienced engineers, production capabilities have expanded substantially from standard bolts and screws into custom cold headed fasteners and component manufacturing. This has provided an unlimited amount of applications where cold headed components can be utilized: aerospace, battery, oil and gas, automotive, and waterworks.
New technology and manufacturing companies are requiring more and more specialized fasteners to manufacture their products, and it’s not something you can find at the hardware store — that’s where custom cold heading steps up to the plate. Adding secondary processes to cold headed blanks, intricate and complicated machined alternatives can also be manufactured at a lower cost.
Here are just a few of the additional processes that can compliment cold heading production:
- Drill and tap
- Knurling and thread roll
- Stamping
- Heat treat
- Plating
- Grinding and shave
- Metal finishing & polishing
- CNC milling
With the help of 2D, CAD, 3D solid modeling, and other engineering software, customer-specific parts can be manufactured to the spec while holding the same tolerances of the machined counterpart. Cold heading can achieve multiple upsets, extrusions, backwards extrusions, many head configurations, and thousands of near net shapes.
Cold Heading Materials
Common cold headed materials range from low to medium carbon steels to copper and nickel alloys. As these parts are formed, the material flow is enhanced through the hammer and die process, which creates a stronger component than its machined counterpart.
Cold heading is limited to certain types of metals. Extremely hard or brittle metals will crack or break tooling on the machines. High carbon steels and super alloys are generally not cold headed due to their extreme hardness. However, required tensile strength and hardness is achieved through heat treatments and the cold working process. A general list of cold headed materials includes (but not limited to):
- Aluminum
- Brass
- Silicon bronze
- Copper
- Monel
- Stainless steel
- Normal carbon and alloy steels
- Other exotic metals
Custom Cold Headed Fasteners – Making the Switch
If you’re a buyer, then you are familiar with the risks involved with making any changes in the supply chain, especially when introducing new suppliers. You could lose quality, on time delivery, efficiency, profit, and ultimately your own customers. But what kind of risk is involved with purchasing a superior fastener or component, at a better price, made specifically for you?
So the buying price alone is not enough on its own to make a decision. How about being able to manufacture an improved product design for the same cost? Or, combining multiple parts into a single component? You can even reduce the overall weight of a part, with no affect on function and save on freight. If you’re looking for an economic solution for today’s manufacturing, then consider custom cold heading as your solution to cost.
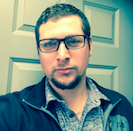
By: Derrick Pledger
Inside Sales and Marketing
Phone: 479-489-5168